一人に1台ずつ、おもちゃ収納ワゴンをプレゼント
「自分が子供のときはこんなにおもちゃ持ってなかったよなー」なんて思いつつ、親戚からもらったおもちゃや誕生日&クリスマスごとにプレゼントしたおもちゃで我が家は溢れかえっている。もともと、妻のしつけが厳しい!?こともあり、子供も片付け上手だとは思っているが、長さ1800mmの板(エルボード)を2枚重ねただけのラックでは、大小様々な大きさのおもちゃを効率よく片付けるのも難しくなってきた。
日頃、いろんな方々のDIYに関するWebサイトを拝見させていただいているのだが、その中で、VIC’s D.I.Y.さんのWebサイトにあった作品集にワゴン型収納棚というものが掲載されていた。これを自分なりにアレンジすれば子供のおもちゃ収納ワゴンとして利用出来るのではと考え、今回はこのワゴン型収納棚から棚板構造の部分に関するアイデアをいただくことにした。その他の作り方は自分流で行っている。なお、VIC’s D.I.Y.さんのWebサイトを見ればわかるとおり、大きいものから小さいものまで様々なものを自作されている方で、参考になる情報もたくさん掲載されている。「読者の作品」なんかは非常に辛口のコメントもあり、今の自分ではとても投稿できない。興味のある方は一度サイトを覗いてみると良いと思う。
7月末が長女、8月上旬が長男の誕生日。これに間に合うように全く同じものを2台作って1台ずつプレゼントする。
【記事補足】
- 以下、製作記になりますが、全般的に写真の写し方/写り方がよくありません。
- 「ベランダ木工」をしながら写真を取っているため、撮影時の日当たり等により綺麗な写真になっていません。
- 写真の背景に生活感が溢れています。。。
基本構想
低コストでの作製と加工の容易性を考慮し、600*300mm(9mm厚)のシナカットベニヤをベースに全体のサイズ設計を行う。高さが高すぎると、子供が一番上のスペースに収納したり、ワゴン自体を動かすときに倒れやすくなったりするため、700mmぐらいの高さになるように設計を行った。また、前回作製したミシンセット収納ワゴンの残り板を有効活用するとともに、効率的な板取も考える。
フレーム部分には1*4(1*6)などのSPF材は利用しなかった。というのも、ホームセンターで販売されているSPF材をよく見ると分かるのだが、どの板もソリがあって、真っ直ぐな状態での「これだ」という板がなかなか見つからない。ひどい時は店頭にあるSPF材すべてが曲がっていることもある。さらに、これらSPF材は角が少し丸くなっていてるため、縦方向と横方向に板を繋ぎ合わせるとき、角の丸い部分が原因で接合部分にわずかに窪みができてしまう。これをなくし、接合部分を少しでも”ツライチ”に揃えられるような角材はないかと考えた。
そこで思いついたのが、400mmとか600mmとかの幅広のパイン集成材をホームセンターで縦方向にカットしてもらうことで、切断面が完全な角材でしかも直線が確保されている板として利用する方法だ。集成材なので強度的に少し心配なため、フレームの縦方向には40や60mmではなく、90mm幅での設計を行うことにした。
設計
ベースは他人のアイデアそのものだが、より使いやすくするために、そして容易に作製しやすくするために、自分流にアレンジを行っている。
- フレームとなる部分はSPF材ではなく、パイン集成材を切り出した90mm、60mm、40mm幅の3種類を組み合わせる。軽量化を図るため厚さは18mmではなく、14mmを利用する。
- 一番下の固定板はキャスターの取り付けと、強度確保のために少し厚めの18mm厚のパイン集成材を利用する。
- 一番上の固定板は、軽量化を図るため、600*300*9mmのシナカットベニヤを利用する。
- 可動棚板は600*300*9mmのシナカットベニヤをなるべくそのまま加工せずに利用する。ただし、長さが600mmだと内寸が600mmであるため、棚板が完全に動かなくなってしまう。そこで、カンナで1mm程度削って幅599mmの棚板として可動しやすくする。
- おもちゃとワゴンの高さを考慮し、まずは棚板3枚とする(もちろん、後から追加も可能)
- 棚板を支える板は60mmと30mmを交互に組み合わせ、棚板の間隔の自由度をある程度確保する
- 一番上の部分にも高さのあるおもちゃを置くことができるようにする
- ワゴンの移動時に邪魔にならないようにフロント、リアともにツライチとする
- 棚板の前後に付ける落下防止板を含め、ホームセンターでのカット依頼が容易な板取りを心がける
- 少し重いものは一番下に収納するが、子供が出し入れしやすいようにフロント側には落下防止の板を取り付けない

この「パイン集成材カット工法(勝手に名付けた)」がうまく行けば、今後はSPF材ではなくパイン集成材をカットしたものを使って工作をしていきたいと考えている。まずは、子供用おもちゃ収納ワゴンを作製してみてからだ。
材料を調達する
設計図をもとに、一つ一つのパーツをコピー&ペーストしながら、取りこぼしのないように板取を行って行く。設計図ができてからというよりは、設計図を書きながら並行して板取図の作製も行う。無駄な板が発生したり、逆に足りなくなったりすることがないようにするためだ。この設計はどんな作品でも同じ手法で行っている。
日頃、ホームセンターで材料調査というか、木のサイズ&価格をスマホで写真撮影して、何か設計するときの情報としてストックしているのだが、幅の広いパイン集成材の在庫調査/価格調査をしていなかった。多分、600mmのものがあった”はず”という考えのもと設計を進め、購入に行ったのだが、実は600mm幅はなく、一番広いもので400mmだった。自宅へ引き返して、設計をやり直し、後日購入にまた行くのも面倒なので、急遽、ホームセンターのカットコーナーに置いてある紙で板取の計算をやり直し(パネルソーの鋸厚3mmを考慮)、そのまま400mm幅のパイン集成材を購入&カットを依頼した。ここにある板取図はカット後に改めて作製したものであり、いつもとは順序が逆になってしまっている。
また、パイン集成材といってもメルクシパイン、ノッティパイン、ラジアタパインなどのように複数の種類が販売されている。過去の経験などから釘や木ネジを使っても割れにくい(と感じた)ラジアタパインを利用した。しかし、割れにくいということは、材質が柔らかいということでもあるので、先程も記載したが強度的に少々不安なところもあったりする。

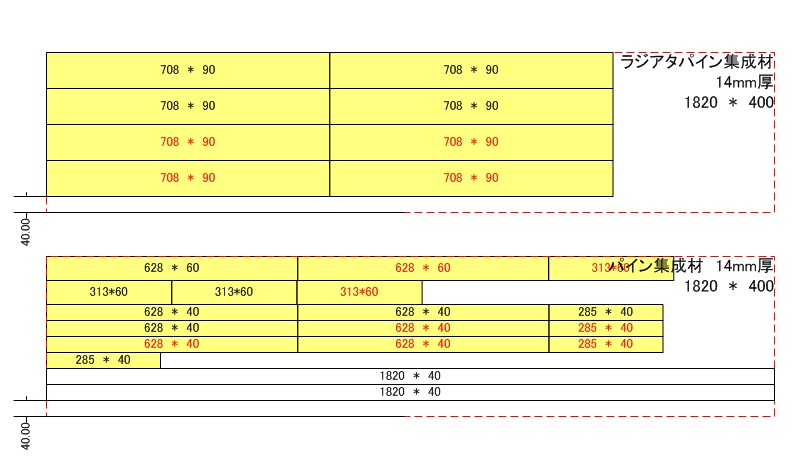
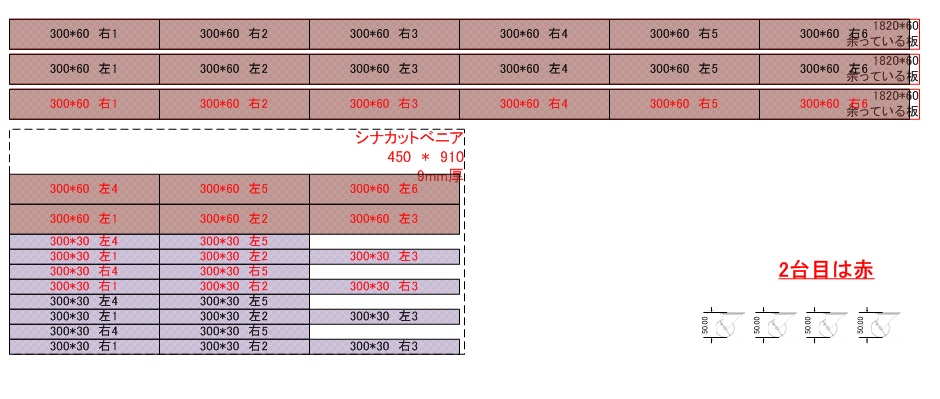
ちなみに、ホームセンターでカットを依頼するときのカット依頼図は今回掲載していない。ここにあるものをベースに、「もし、同じ幅のものがもう一枚取れそうだったらお願いします」のような感じで説明してカットしてもらった。ちなみに、ラジアタパイン材を購入&カット依頼したホームセンターのおじさんは、いつも非常に親切に対応してくれる。一方、シナカットベニヤを購入&カット依頼した別のホームセンターの店員さんは「ハズレ」の方が担当だと非常に無愛想だったりする。現に、自分の後に1枚板を持ってカット依頼に来ていた女性はうまく説明ができなくて、相手がお客さんなのにイライラ感が全身から溢れでた対応をしていた。もう少し丁寧な接客をお願いしたいものだ。
棚板を支える部分の準備
最初に大量に必要となる棚板の支え部分の加工から行った。ワゴン1台あたり、60mm幅のものが12個、30mm幅のものが10個必要となり、2台分作製するため60mmと30mmを合計すると、なんと44個も必要となる。また、60mm、30mmとも長さ(奥行き部分に該当する)は300mmであり、全て手作業となるため、1枚1枚個別に鋸でカットしてしまうと、全部そろったときに微妙に長さが異なってしまう可能性が高くなる。そこで、ある程度の枚数を重ねた上でカットすることで、長さ300mmに対するブレ(誤差)を最小限に抑える。
カットの終了後、こすったときに指をけがしたりしないようにカンナ掛けと240番の紙ヤスリで研磨仕上げをしておく。この作業も複数枚の板を重ねて作業することで、なるべく個体差が発生しないようにする。
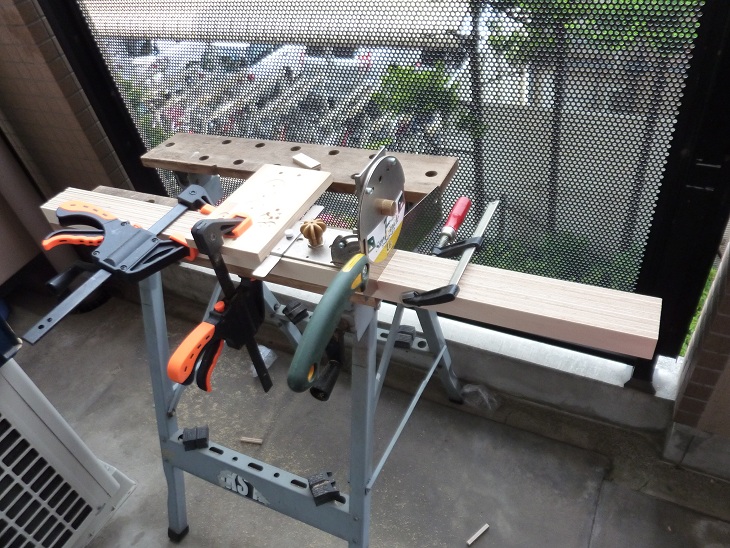
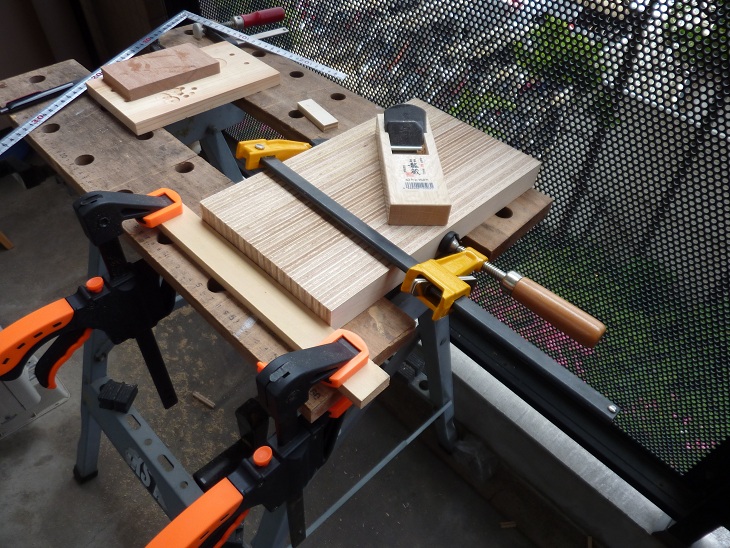
フレーム部分のカット&加工
フレーム部分(外枠)も同じ長さが複数個あるものについては、まとめてカットする。ただ、厚さが14mmあり手作業でのカットとなるため、2枚まとめてでのカットが限界だ。さすがに4枚重ねはきつそうだ。
縦方向のフレームについては、横方向のフレームと接合する部分、すなわちちょうどワゴンの四隅に当たる部分を写真のような形状にカットする。縦引き鋸を所有していない中で縦引きを行わなければならず、非常にやりづらくゆっくりとしたカットになる。また、ソーガイドをクランプで固定するにしてもソーガイド本体と木材の重なる部分が少ないというスペース的な制約があるため、慎重に作業を行う。
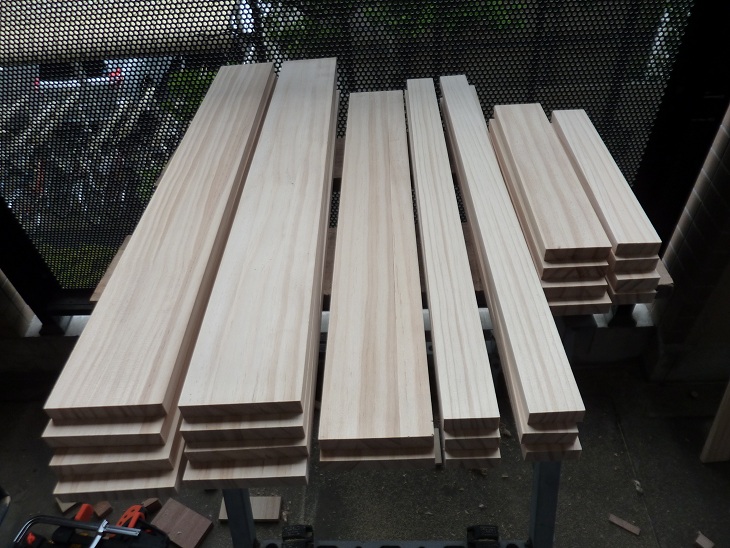
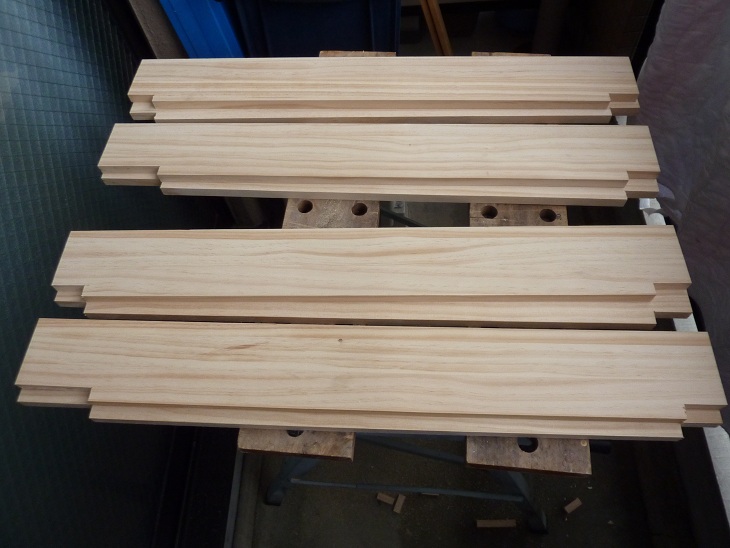
フレームを組み立てる(前後それぞれ)
フレームを組み立てていくが、直角の精度が得られていないと組みあがったときに傾いたり、棚板との建て付けが悪くなったりする。前回作製したミシンセット収納ワゴンでの失敗を生かし、今ある道具でなんとか直角を出す方法はないか考えた。道具ではないが、今回購入している600*300mmで18mm厚のラジアタパイン集成材にフレームとなる板がぴったりくっつくように組み立てることで、ほぼ90度に近い直角が得られそうだ。
ラジアタパイン集成材にフレーム部分を載せた状態で、木工用ボンドと隠し釘を使って固定し、その後、木ネジでさらにがっちりと固定した。これを1つのフレームに対して上下繰り返し、1台あたり2セット分、合計4セット分作製した。
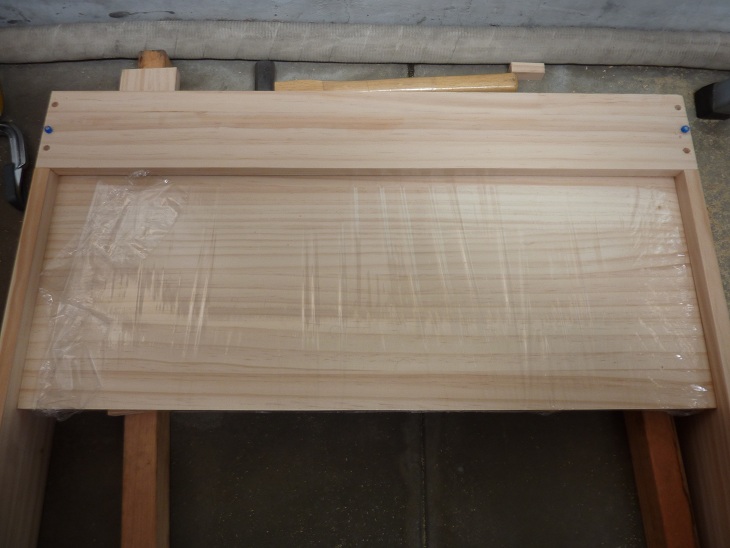
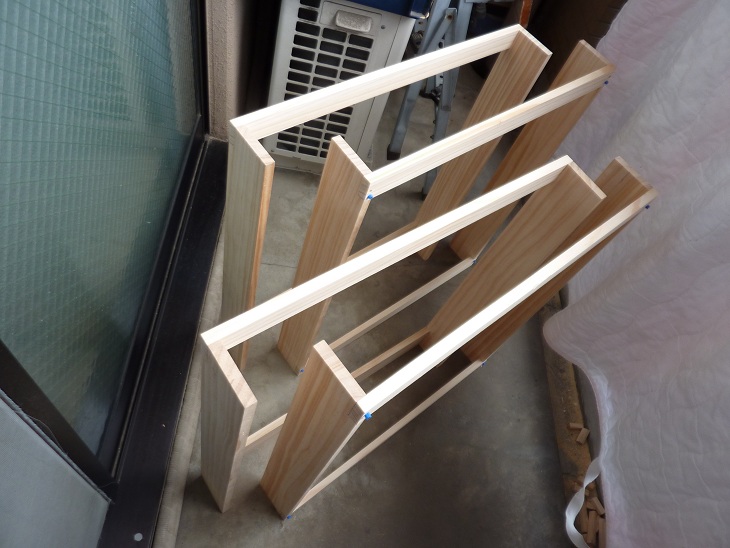
フレームの前後の接合
組みあがったフレームの前後にあたるパーツを接合するわけだが、一番上の部分に位置するフレームのカットを忘れていたことに気づく。ここでも面倒な縦引きが多く発生し、直線切りが簡単にできる電動工具が欲しいなと思いつつ、地道に作業を進めた。
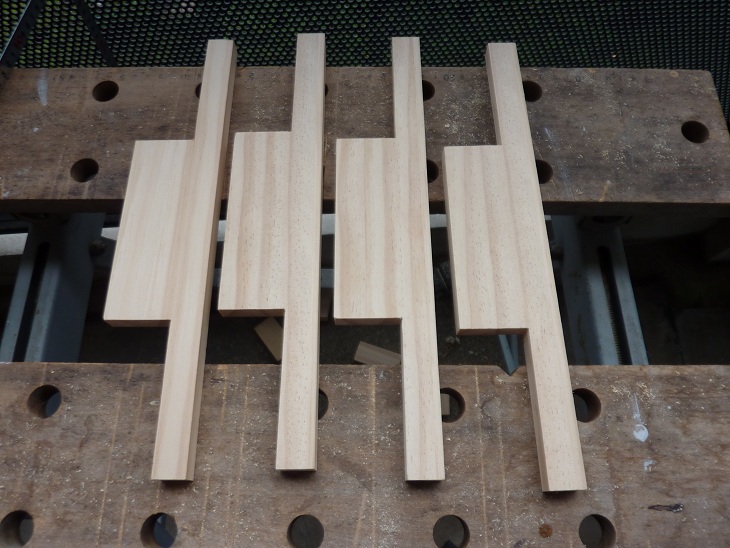
縦/横方向のフレーム間には木ダボを利用して接合する。フレームどうしの面をそろえ、段差が出来ないように注意する。構造上、縦方向の接合は同じようにダボ接合が利用できないため、フレームの上から深さ5mm程度の穴をあけ(6mm木工用ドリル利用)、木ネジで固定したあと、丸棒で表面を整える方法を採用している。一番下の部分はカットした281mmのフレームにぴったり前後がくっつくように接合する。281mmという寸法と、この材料の直角が出ていることを信じての作業となる。
一番下の18mm厚の固定板(ラジアタパイン集成材)は設計上295mmの奥行きにしないといけないが、購入した18mmのラジアタパイン材は300mmの奥行きがある。そこで、仮組みしてから現物合わせで飛び出してしまっている部分に沿って線を引き、この5mm程度の幅をカットして、フレーム内にぴったり収まるように調整する。これも600mmという長さにわたって縦引きカットをしなければならず、非常に苦労した作業の一つとなった。電動工具があると楽なんだけどなー。
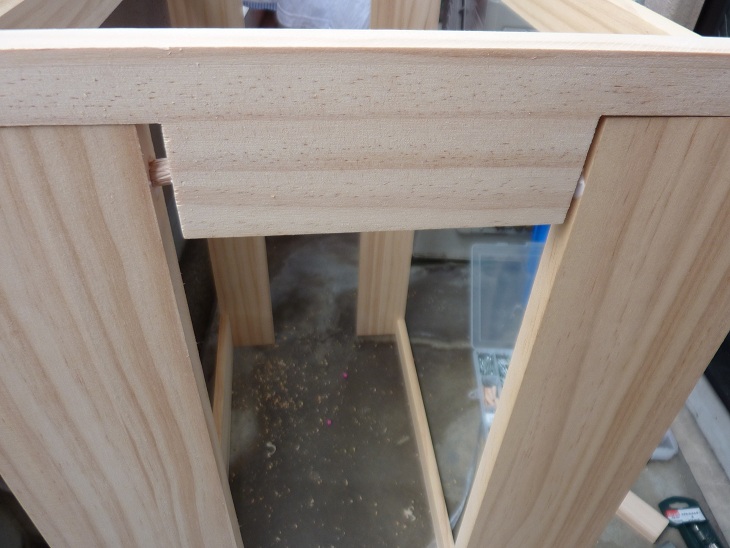
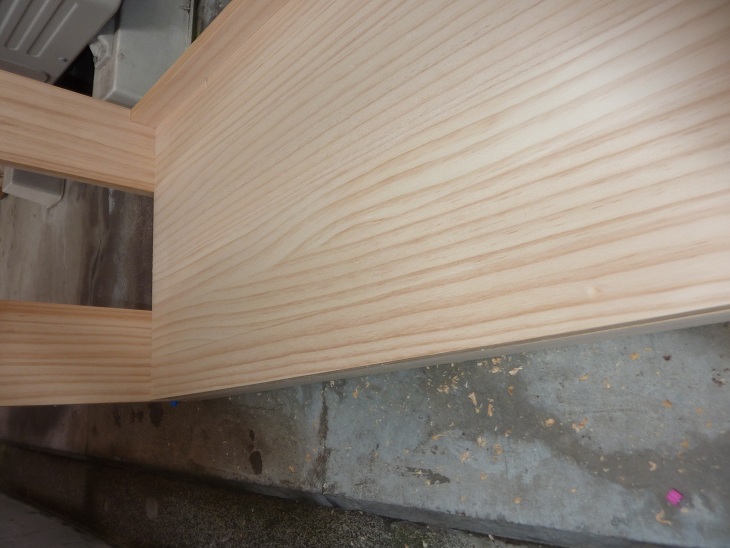
フレームを組み立てた後、100番のサンドペーパーで全体的に角を少しだけ削り、子供が手をけがしないようにした。また、一番上の角の部分は、写真のようなR加工を施した。これもすべて手作業での実施である。10mmの二等辺三角形ぐらいの大きさで角の部分をカットし、あとはひたすら100番のサンドペーパーで削っていく。サンドペーパーを小さな木材に丸めて削ることで力を加えながら削れるようになるため、写真のようにある程度の丸みは出せる。
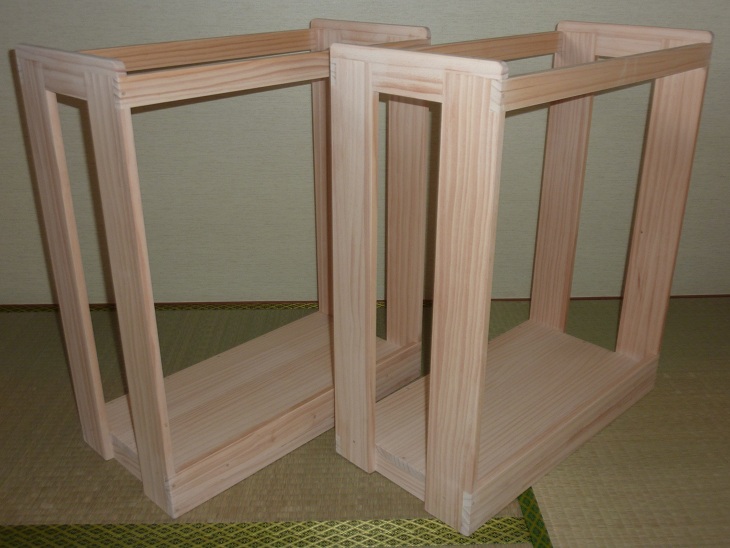
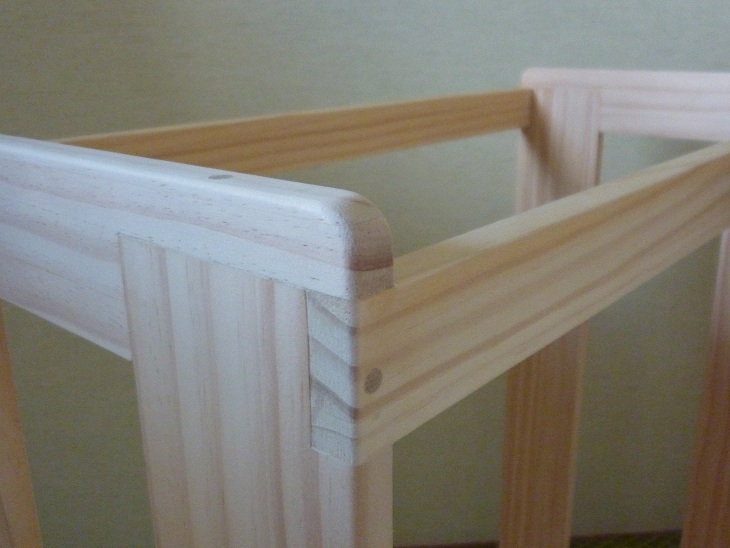
棚板の作製
棚板は600*300mm(9mm厚)のシナカットベニヤを利用する。600mm幅のままだとフレーム部分の内寸と全く同じ大きさになってしまい棚板自身が可動しなくなってしまう。そこで、片端を1mm程度カンナで削りスライドさせるための遊びを左右に確保する。ベニヤ合板なのでカンナで簡単に削ることができる。
また、棚板はおもちゃが落下しないように前後にストッパーとなる20mm幅の板を取り付ける。取り付け方法が前後で異なるため、前から見た場合と後ろから見た場合でストッパーの高さが異なるようになる。これは、できるだけ同じサイズの材料を利用したのと、フロント側はストッパーの高さが低いほうがおもちゃの出し入れがしやすいことも考慮したためだ。リア側のストッパーは棚板が左右平行に移動するための機能も担っており、棚板を支える板の厚み9mmを考慮してフロント側よりも短い長さとなっている。
フロント側、リア側とも木工用ボンド+隠し釘で固定した後、長さ16mmの木ネジ+丸棒整形を行う。ベニヤ板は柔らかくて加工がしやすいのだが、逆に割れや角の欠けが発生しやすく、取り付け時のドリル穴加工や木ネジの打ち込みはかなり慎重に行わなければならない。実際に角が少し欠けたり、木ネジがセンターから少しずれただけでも表面が盛り上がって波打ったりしてしまう。コスト的に問題なければベニヤ板以外の木材を利用したほうが良いと思う。
2台分、合計6枚の棚板セットを作製した。作成後、手に擦り傷を作ったりすることがないように、前後のストッパー部分にだけ、水性ウレタンニスを塗った。棚板部分は可動のしやすさを確保するため、ニスは塗っていない。ニスを塗ってしまうと、たとえ乾いた後でもくっついてしまいそうな気がしたためだ。
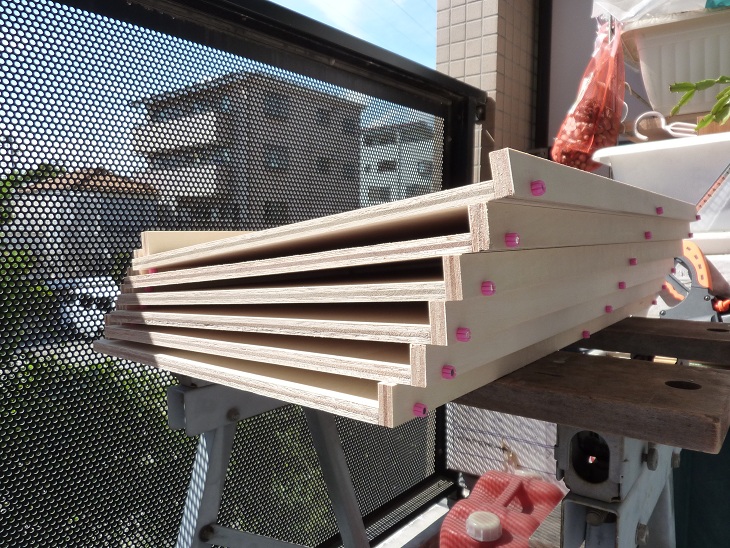
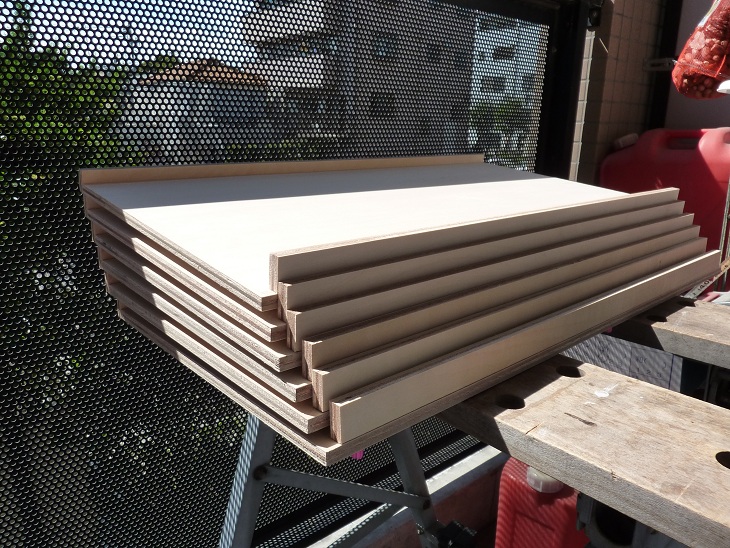
一番上の固定棚板をフレームに取り付ける
この部分は設計上は奥行き281mmとなる。600*300mmのシナカットベニヤを利用することになるため、実際にフレームにこの板を仮組みしてみて、フレームにそって余分な部分をカットするための線を引き、ソーガイドでカット、カンナで研磨、100番のサンドペーパーで研磨を行って現物合わせで寸法を出していく。その後、上側の横方向フレームの底面とこの板の底面が揃うようにして木ネジで固定していく。最後にいつものように、丸棒を使って表面をきれいにする。
この段階でフレーム部分全体に水性ウレタンニスを2回塗って、240番のサンドペーパーで研磨、さらに最後にもう1回、水性ウレタンニスを塗っておく。棚板を支える部分の板を取り付けた後、全体にニスを塗ってしまうと、棚板をスライドさせようとしたときに乾いているとはいえ、ニスを塗っている部分がくっついてしまいスムーズに可動しなくなってしまう恐れがある。そのため、今回はフレーム部分以外のところにはニスを塗らないことにした。実際に、前回作製したミシンセット収納ワゴンでは引き出し部分を可動させるときに乾いているはずのニスがくっついてしまい、可動させるために少しコツが必要となってしまっている。
なお組立工程全般で言えることだが、手作業でのカットのため木材の接合部分にわずかながらではあるが隙間が生じてしまうことがある。そんなときは、木工用パテを塗りこみ、すぐに濡れ雑巾で拭き取る。こうすることで、隙間部分にはパテが残り、それ以外は木材の表面のままとすることができて、見た目にも非常に綺麗な仕上がりとなる。ただし、すぐに拭き取らないと余計な部分にパテが残ってしまい、木材の色との微妙な違いがかえって目立つ結果となってしまう。
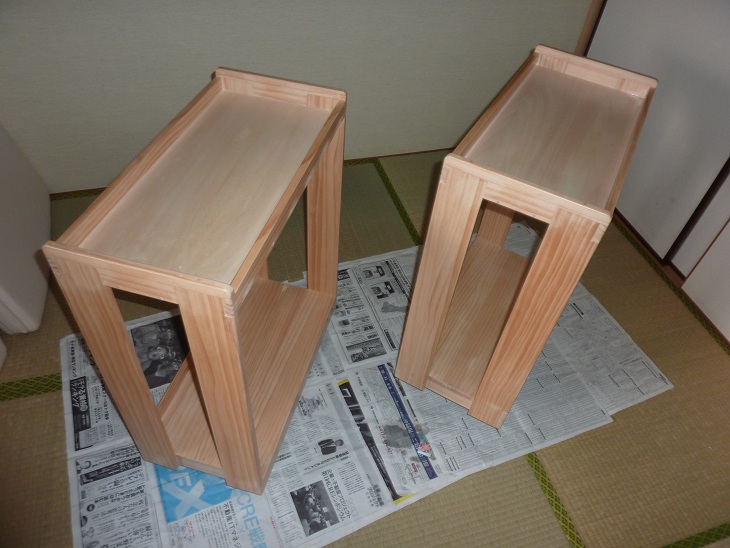
棚板を支える板の取り付け
最初の工程で、加工を終えていた棚板を支える板(60mmと30mm)をフレームに固定していく。設計図にしたがって、フレーム内側に取り付け位置をマーキングしておき、そこに合わせて木工用ボンドで接着していく。このとき、フロント側が綺麗に揃うように、9mm厚のシナベニヤ材をフロントとツライチになるように合わせながら、棚板支え板を固定していく。
一晩ぐらい寝かせた後、一番下の部分と一番上の部分を現物合わせを行ないながら加工を行う。一番上の部分については、全体の内寸高さが1mm程度設計と狂ってしまっていたため、さらにこの支え板をカンナで1mm程度削ったりしながら、棚板の可動がスムーズになるようにサイズ調整を行った。一番下の部分の四隅でのカット加工も現物合わせでカット寸法を出している。
そして、完全に固定するために木ネジを打ち込んでいく。深さ3mm程度の下穴を6mm木工用ドリルで開けておき、そこに長さ16mmの木ネジを打ち込む。その後、丸棒で表面を整えていく。一番上と、一番下については隣接する固定棚板を支えるための強度を確保するためにも+2本多い、合計6本での固定とした。結果、1台あたり、96回の取り付け加工を行うことになり、2台合計で192回もの加工をこの部分だけで行っていることになる。
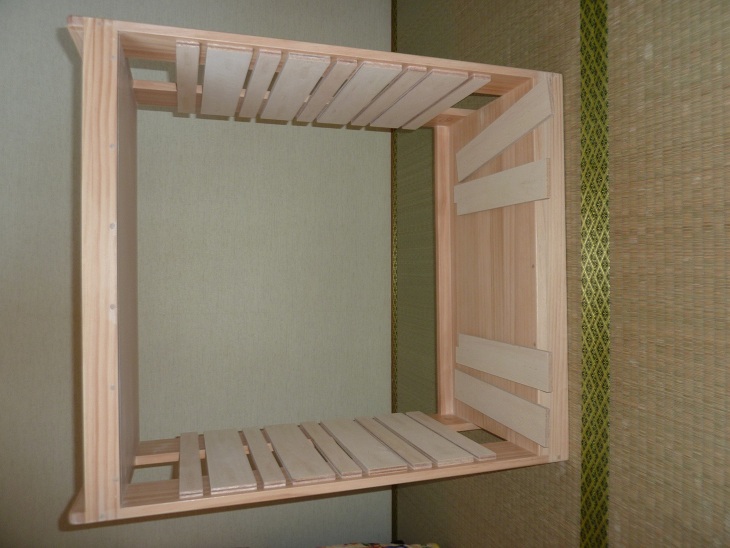
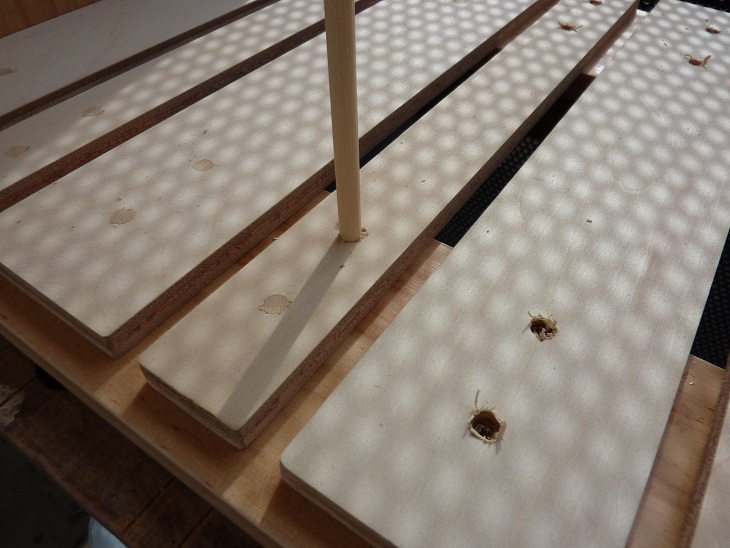
キャスターの取り付け
フレーム作製が終了したら、キャスターを取り付ける。底板(固定棚板)は18mmの厚さがあるが、キャスター取り付け用の木ネジを少しでも長いものが利用出来るように、厚さ4.5mmのシナベニヤの廃材をキャスター取り付け時に挟む。これにより長さ18mmの木ネジを利用することができ、表からネジが突き抜けることを防げる。キャスターは側板から5mm程度のスペースを確保する感じで取り付けを行った。ちなみに、利用したキャスターは取り付け高さ50mmのハンマーキャスターだ。
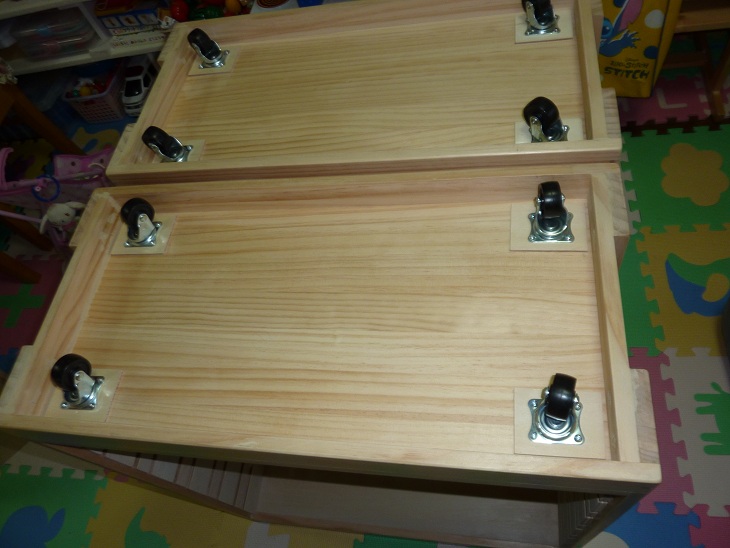
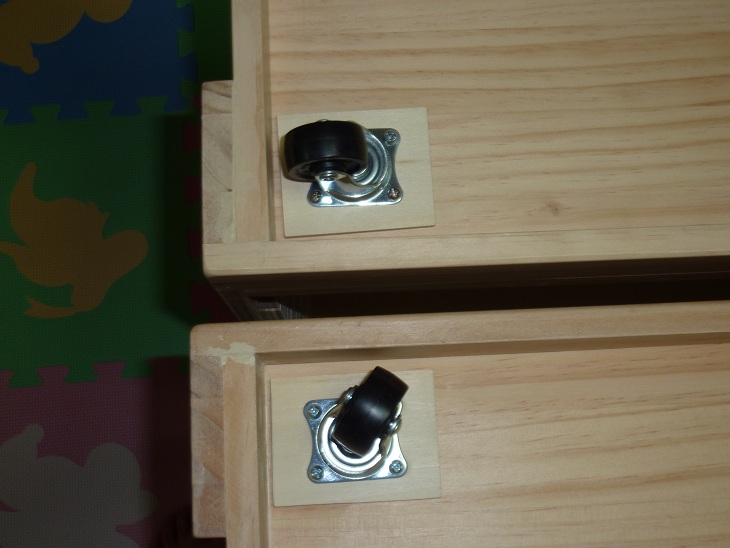
そして完成
棚板を適当な高さに取り付けて仕上がり具合を確認する。収納するおもちゃのサイズにあわせて棚板の位置は後から変更する。実際に棚板を可動させると、内寸幅600mmに対して棚板の幅599mmであるため少しだけ棚板の出し入れにコツが要るが、それほど突っかかるような感じもないのでこれで完成とした。
最後の写真はおもちゃを収納したところだ。二人の子供はこのワゴンを作製途中の段階からどんなおもちゃケースが出来るのだろうと非常に楽しみにしてくれていたこともあり、完成後はとても喜んでくれた。ただ、小さい子供にとってはワゴン自体を簡単に動かすことがなかなか難しい様子で、今の段階では写真のように固定設置の状態になっている。
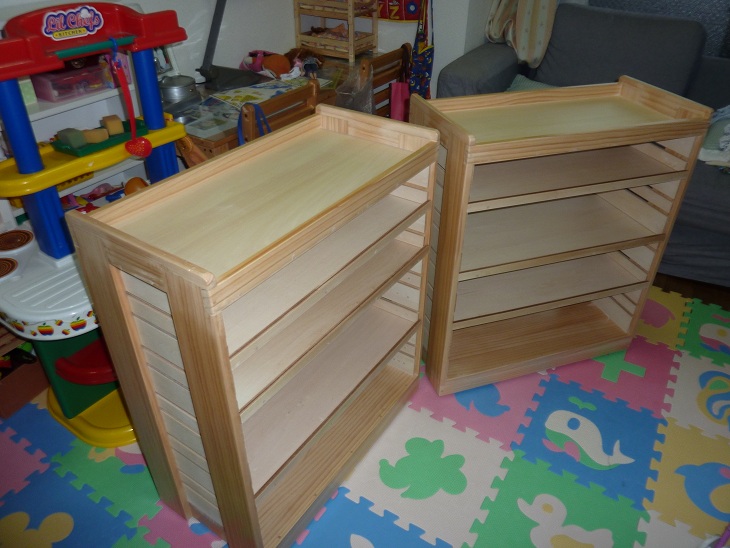
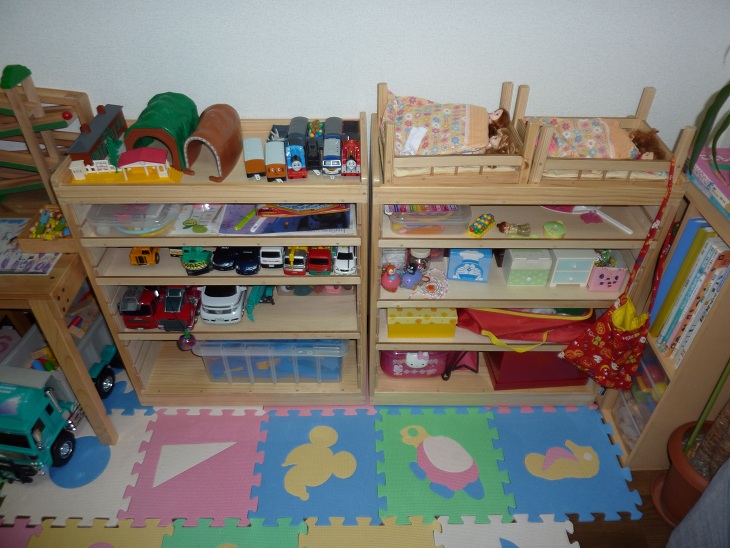
製作費用は
今回の製作費用を最後に。過去の製作時の残り板利用分、木ネジ・ニス・工具など共通的な費用(ストック品の利用分)は含んでいない。工賃は恒例の「プライスレス」だ。
材料 | 用途 | 数量 | 価格(合計) | 購入方法 | コメント |
---|---|---|---|---|---|
シナカットベニヤ | 棚板支え板 | 1 | 1,150 | ホームズ | 450*910*9mm。ミシンセット収納ワゴン作成時の余りとあわせて利用。 |
シナカットベニヤ[A] | 棚板の落下防止板 | 1 | 528 | ホームズ | 600*300*9mm |
[A]のカット料金 | – | 23カット | 1,150 | ホームズ | 1カット50円 |
ラジアタパイン集成材[B] | フレーム部分 | 2 | 6,560 | ドイト | 1820*400*14mm。単価3,280円 |
[B]のカット料金 | – | – | 480 | ドイト | – |
ラジアタパイン集成材 | 一番下の固定棚部分 | 2 | 1,796 | ドイト | 600*300*18mm。単価898円 |
シナカットベニヤ | 棚板部分 | 6 | 3,168 | ホームズ | 600*300*9mm |
シナカットベニヤ | 一番上の固定棚部分 | 2 | 1,056 | ホームズ | 600*300*9mm |
キャスター | – | 8 | 1,344 | ホームズ | 取り付け高さ50mmタイプ。単価168円。意外と安い |
丸棒 長さ910mm/6mm径 | 木ネジ打ち込み後の整形用 | 2 | 136 | ホームズ | 単価68円 |
ストックからの利用 (主なもの) | ・隠し釘 ・木ネジ ・木工用パテ ・木工用ボンド ・水性ウレタンニス | – | – | – | ウレタンニス、木ネジなど、追加購入したものも多い |
– | – | 合計 | 17,368 | – | 1台あたり8,684円 |
意外にコストがかかってしまったというのが率直な印象だ。ニスや木ネジ、サンドペーパーなど今回追加で購入したものを含めると、軽く合計20,000円はオーバーしてそうだ。コスト削減のためにシナベニヤ板を多用したが、一番上の固定棚部分と、各棚板に取り付けた前後の落下防止用板の部分だけはベニヤ板ではなくもう少ししっかりした板を利用すべきだった。
なお、パイン集成材を切りだして、SPF材のようなイメージでフレームとして利用したが、当初懸念したような強度不足もなさそうで、このようなDIYにも有益であることがわかった。材料も直線が確保されているため、板を購入するときに選択に悩む必要もない。また前回のミシンセット収納ワゴンで少しミスったような「直角が出せていない、わずかに傾いている」といったことが発生することもなく、綺麗に作製できた。今後、ある程度大きなものを作製するときは、今回のようにパイン集成材切り出しの方法を使っていきたい。
反省点としては、少し風の強い日に作業したときにカンナで削った削り屑がお隣さんのベランダまで飛んでしまっていたことだ。特にクレームが来たわけではないが、これはまずかった。そのうち、管理会社に連絡なんかされてしまってベランダ日曜大工自体もできなくなってしまいかねない失態だ。かなり注意が必要で、かなりの反省だ。
毎度のことながら、完成したら次に何か作りたくなってしまう。プリンタ設置ワゴンか、もしくは木で作った手作りトラックのおもちゃなどの小物類を作製してみようかと考えている。そして、無性に糸鋸盤がほしいと思う、今日この頃だ。